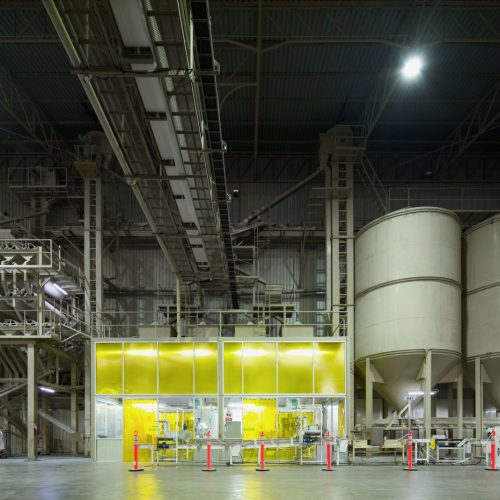
Processing Plant
Our cutting-edge processing plant operates at peak efficiency, capable of producing an impressive 7,000 metric tons of rice daily. Equipped with high-tech machinery, including automatic packing systems and state-of-the-art equipment, our facility embodies innovation and precision.
Our commitment extends beyond production, as we meticulously monitor our processes to minimize social and environmental impact. Rigorous quality control measures and the latest technology are seamlessly integrated into every facet of our manufacturing journey, beginning with the careful selection of raw materials and extending through our production methods, packaging practices, and international shipping standards.
Ware house
Our expansive warehouse facilities are a cornerstone of our operations. With a massive silo storage capacity exceeding 310,000 metric tons, we provide secure and ample storage space to maintain our high-quality rice. Our compound is strategically designed to accommodate large commercial vessels with a deep-water wharf, and it is staffed by highly skilled professionals who meticulously oversee every aspect of production.
To optimize storage efficiency and distribution capabilities, we employ an advanced ERP system, and lays the foundation for even more efficient methods in the future, reflecting our commitment to continuous improvement. Our warehouse facilities are maintained to the highest cleanliness standards, underscoring our dedication to quality throughout every aspect of our operations
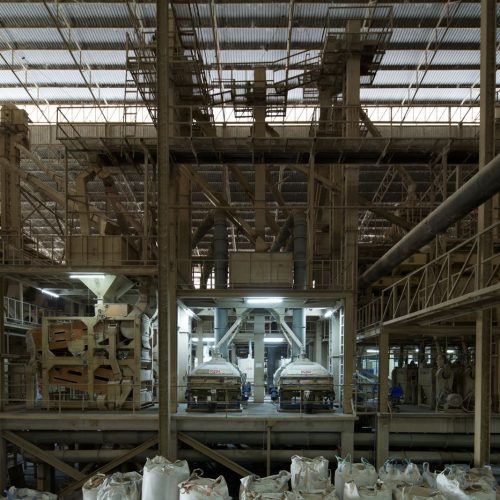
Process
Rice received from millers undergoes an initial sampling to evaluate the quality of the grains, followed by laboratory processes to examine their physical and chemical characteristics. Raw material is then stored in silos to maintain the quality before entering the production process.
After harvesting, rice undergoes a cleaning process to remove impurities and unwanted materials with pre-cleaners, followed by stone removal and separation of heavy impurities using a Destoner.
After the cleaning processes, rice is polished to smoothen the grains, clean out any remaining bran, enhance its appearance, texture, and quality, and give it a shiny surface by passing it through a series of rollers using air and water, allowing it to be stored for longer periods.
Color sorters are utilized to separate yellow grains, remove shocky and damaged grains, and ensure uniformity in appearance by sorting rice grains based on color and defects, resulting in a uniform and single-color product.
Grading is the process of separating rice into different lengths, based on size and quality, which may involve separating one or two kinds of broken or shorter grains from whole grains by length.
Quality inspections include laboratory tests to determine qualities like humidity level, rice coloring, and Amylose count before packaging, along with rigorous assessments of the rice’s moisture content.
Our automated packing system ensures that finished products are contained in outer packaging, meeting customer requirements and maintaining consistent quality standards.
The finished product is packed and stored in our warehouses, which are rigorously maintained to ensure cleanliness and protection against dust and pests, before being delivered to valued customers.
Our finished products are exported from our factory via breakbulk vessels, barges, and containers, with meticulous transportation arrangements to ensure safe and suitable shipping methods to their respective destination.